The old block covers were worn out, and it was time to apply some new leather. We learned there was more to it than first meets the eye.
Dorade sails with nearly 30 wood blocks to manage her running rigging, and they were protected for the last several years with elk-hide covers. Part of last winter’s maintenance regime was not only to replace the covers but also refinish the wood sections of the blocks.
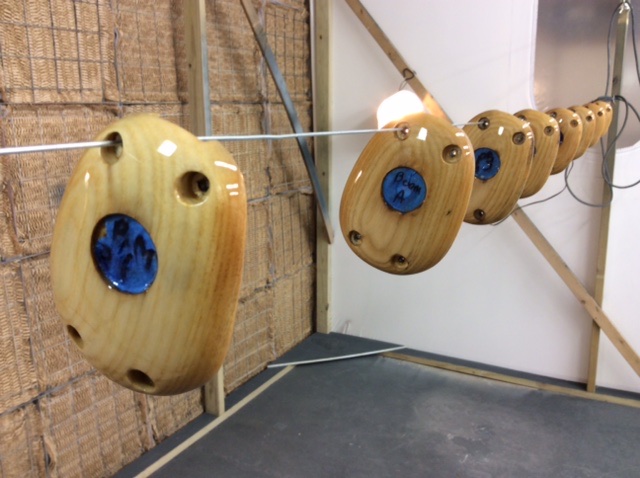
Mike Fletcher (Makai, Inc.) handled the refinishing, and we’ll have more on his extensive work aboard Dorade in a future post. Once Mike had reassembled the glossy blocks, Ted Romanosky took on the task of fashioning the new covers and sewing them in place.
We discussed the process with Ted, early in the spring, and the conversation started with the decision to change materials, swapping out the elk hide for Latigo leather, which is combination tanned and infused with oils and waxes. Ted has used Latigo for other classic boats and says it is resistant to weather but still reasonably flexible. Treated annually, he says, its rich color may darken a little over time.
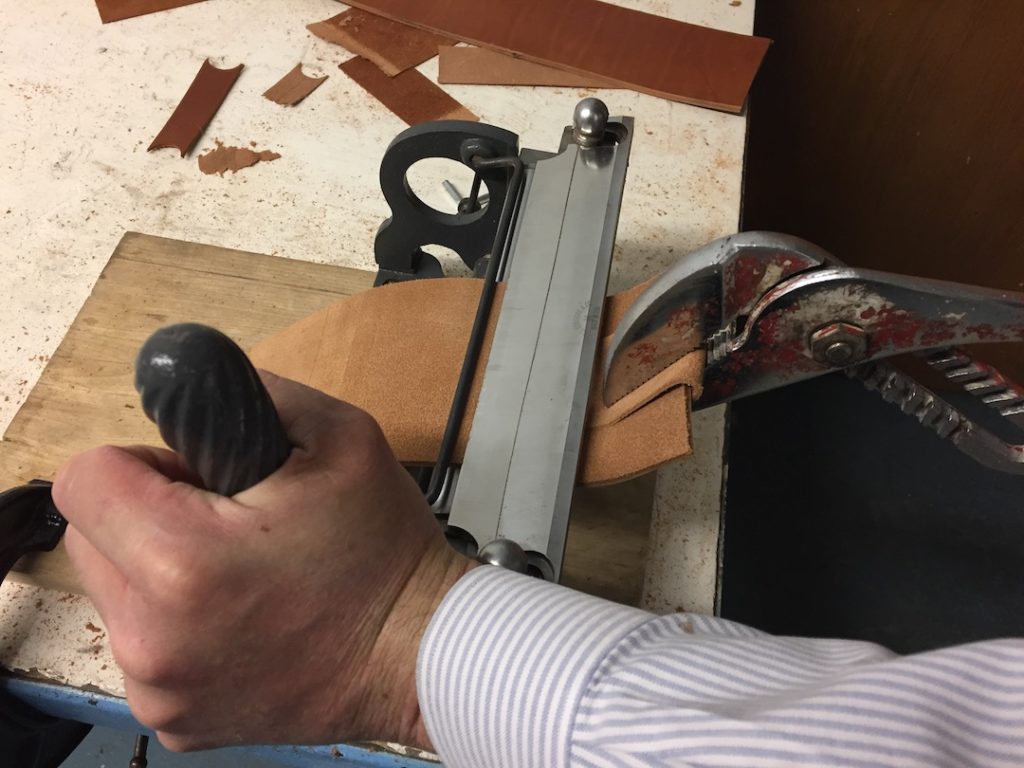
A quantity of leather was hand-selected and amounted to “three sides of cow.” To get the right thickness for each piece, the leather was then split using a C.S. Osborne leather splitter with what Ted described as an “insanely sharp blade.” The machine was designed in 1890 and apparently works as originally intended, with two people pulling the leather through the splitter.
Ted drew patterns for the covering of each size block and cut the leather accordingly. All pieces were waterproofed using mink oil.
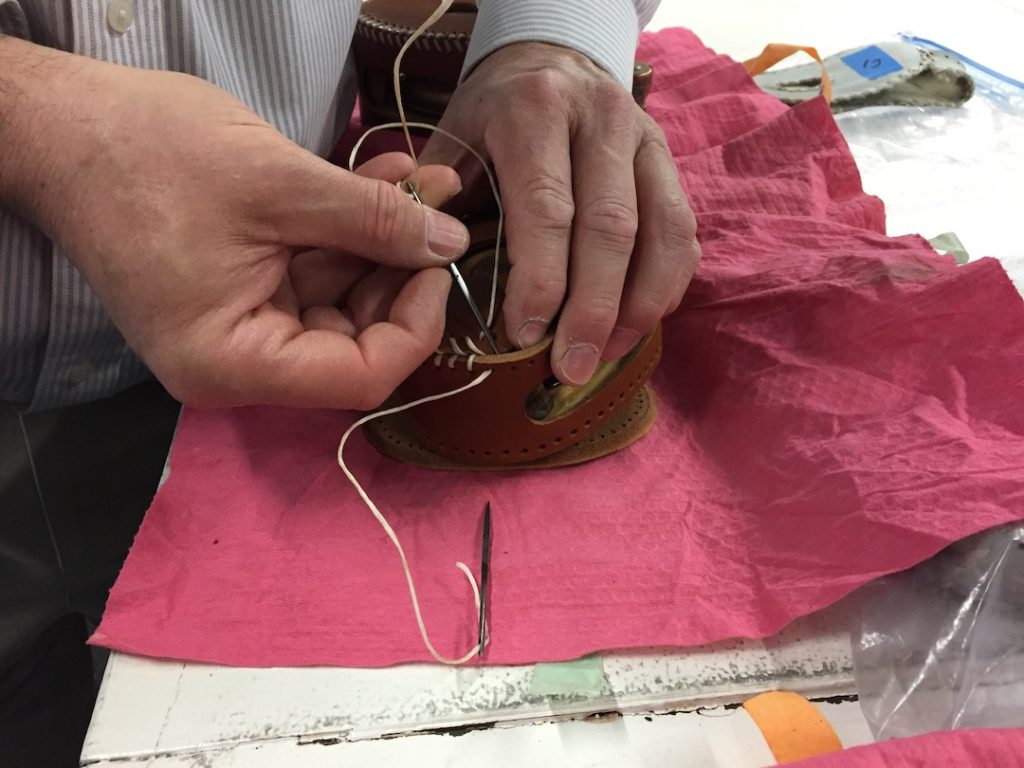
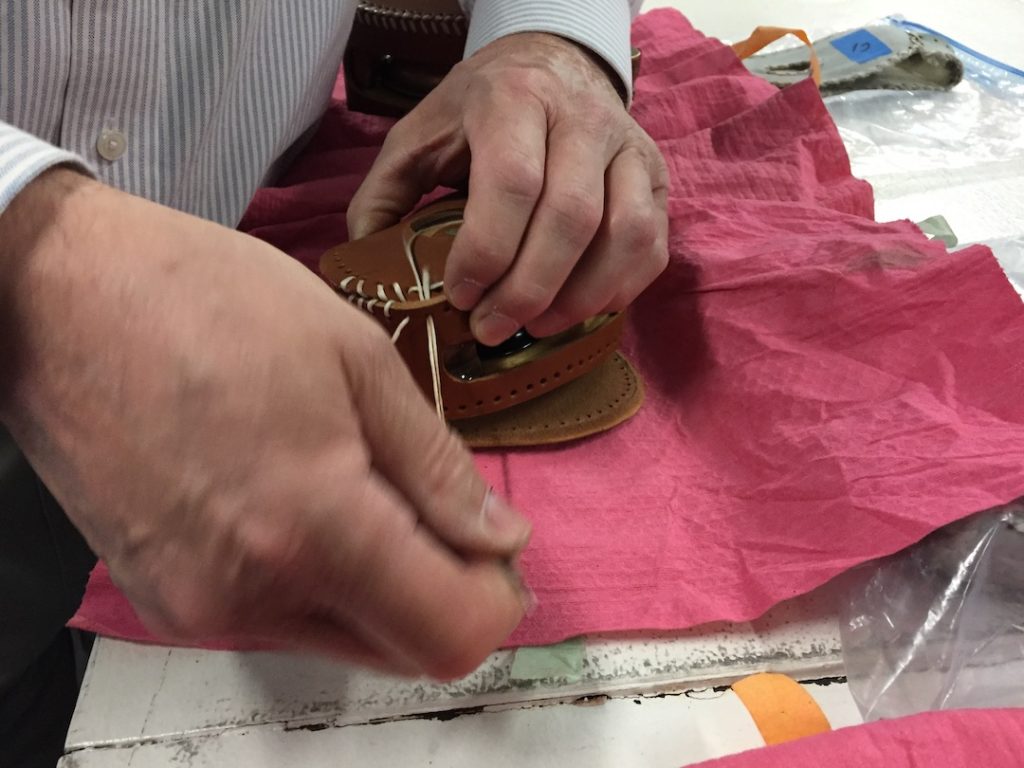
To prevent any turning up at the edges, the strap sections around the block used slightly thicker leather than the shell sections on the sides or cheeks of the blocks. In addition, Ted cut the leather at an angle to create a French bevel where the edges of the leather meet. Depending on the size of the blocks, the straps are 1/8” to 3/32” thick, and the shells are 1/16” to 3/32”.
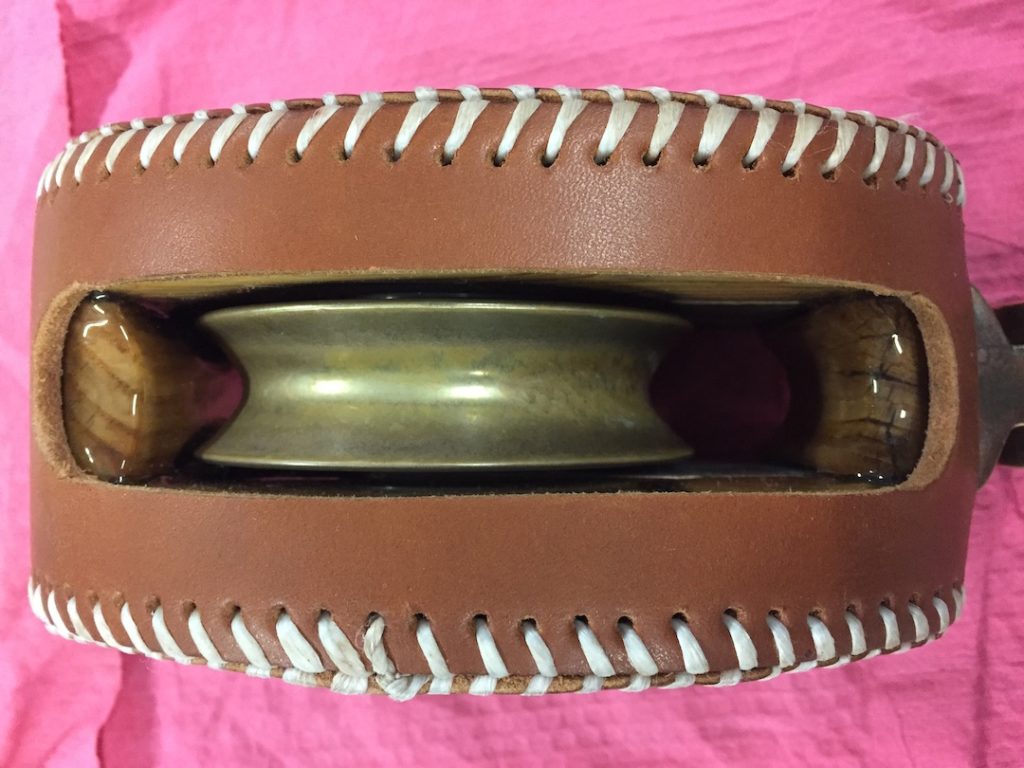
Before he could sew the leather pieces together around the blocks, Ted hand punched holes at approximately quarter-inch intervals. Some people make slits, Ted say, but I think round holes are important because leather has a grain and the circle provides an intrinsic value of strength.
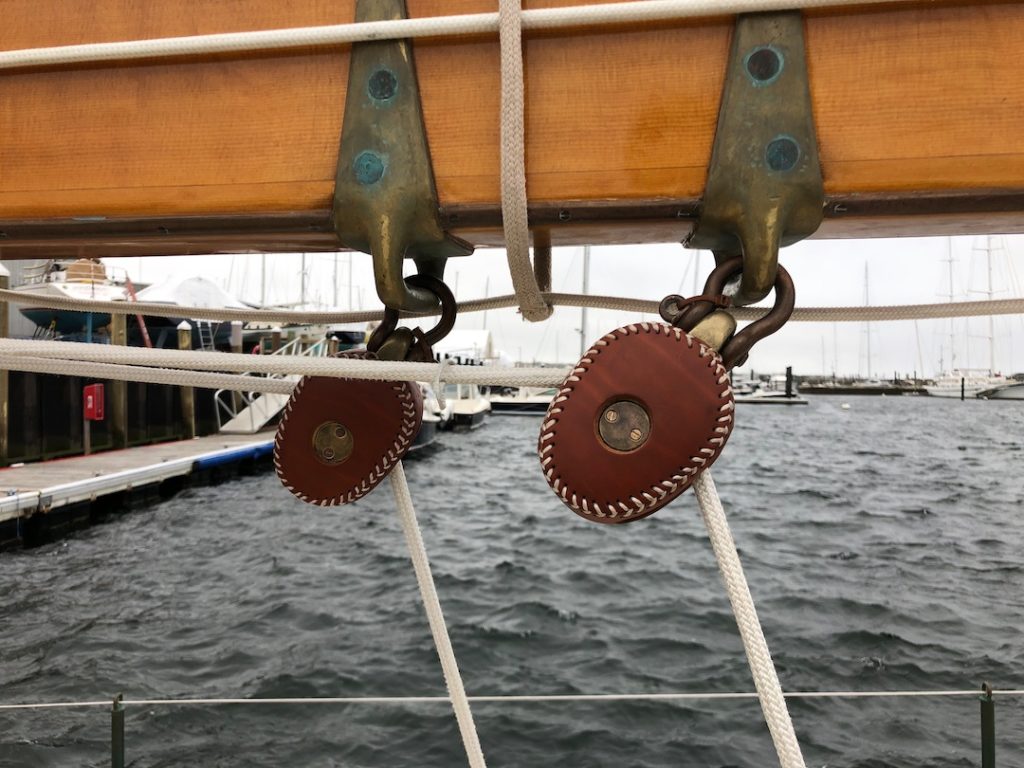
For the stitching, Ted used a waxed twine, sewing with a baseball-style stitch that allowed him to pull the leather tight as he worked around the block. The blocks were finished and delivered to Dorade for her commissioning at the end of April. Now Ted is working on new chainplate covers.